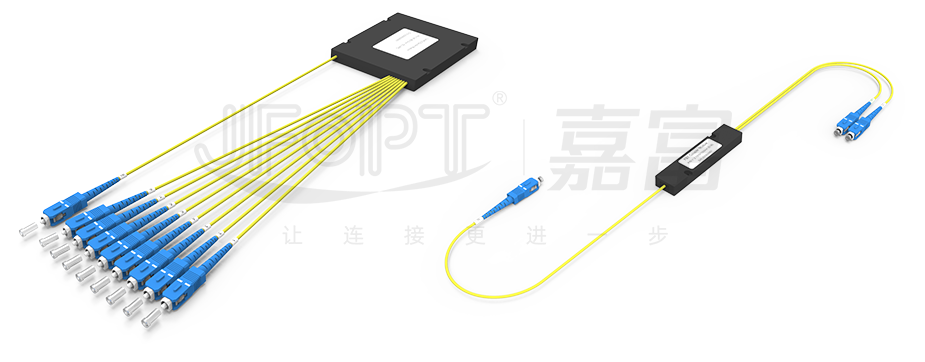
PLC optical splitters are manufactured using semiconductor technology, providing a high-quality solution for applications requiring high splitting configurations. Their working principle involves integrating waveguide structures onto a quartz glass substrate using photolithography technology to achieve specific ratios of optical signal distribution. Common splitting ratios for PLC optical splitters include 1:4, 1:8, 1:16, 1:32, and 1:64. Depending on the application requirements, PLC optical splitters come in various types, such as bare fiber type, mini steel tube type, ABS box type, with branching type, tray type, rack type, LGX optical splitters, and micro plug-in type.
FBT optical splitters use traditional passive device manufacturing technology by bundling two or more optical fibers together and employing a tapering machine for fused stretching to achieve signal distribution. Because the fused optical fibers are relatively fragile, they are typically protected with a glass tube made of epoxy resin and silica, which is then covered with a stainless steel tube and ultimately sealed with silicon. As technology continues to mature, the cost-effectiveness of FBT optical splitters has also improved.
As seen from the above introduction, there are significant differences in the manufacturing processes of PLC optical splitters and FBT optical splitters. In addition, these two types of optical splitters also differ in the following aspects:
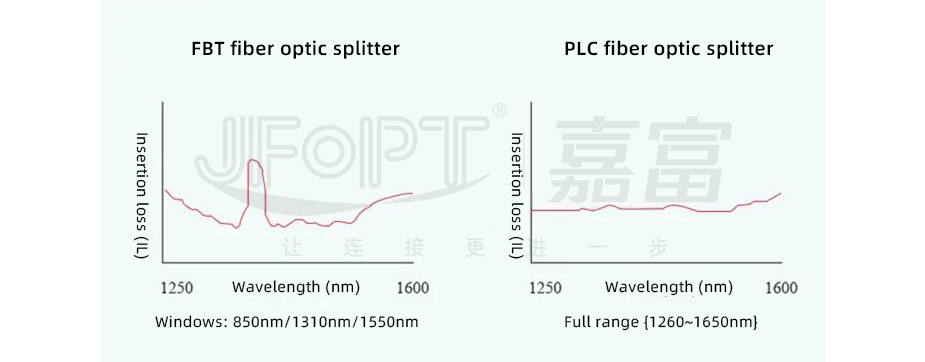
The working wavelength range of PLC optical splitters is between 1260nm and 1650nm, with adjustable wavelengths suitable for a wider range of applications. In contrast, FBT optical splitters only support three fixed wavelengths: 850nm, 1310nm, and 1550nm, and cannot operate at other wavelengths.
▶ Splitting Ratio
The splitting ratio refers to the ratio of the input optical signal to the output optical signals in an optical splitter. PLC optical splitters can achieve a splitting ratio of up to 1:64, offering higher reliability. In comparison, FBT optical splitters have a splitting ratio of 1:32, which is slightly lower than that of PLC optical splitters. However, FBT optical splitters can be customized to various ratios based on needs, such as 1:3, 1:7, 1:11, etc. In contrast, PLC optical splitters only offer standardized splitting ratio options, such as 1:2, 1:4, 1:8, 1:16, 1:32, and 1:64.
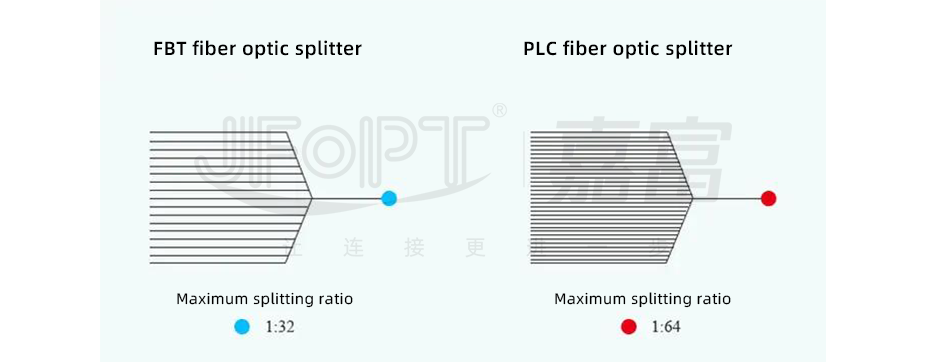
▶ Splitting Uniformity
PLC optical splitters achieve uniform splitting with proportional accuracy, while FBT optical splitters, which are assembled from multiple 1x2 splitters in series, lack effective signal management and thus struggle to provide uniform splitting. As the splitting ratio increases, the uniformity of FBT optical splitters decreases further, which can impact transmission distance.
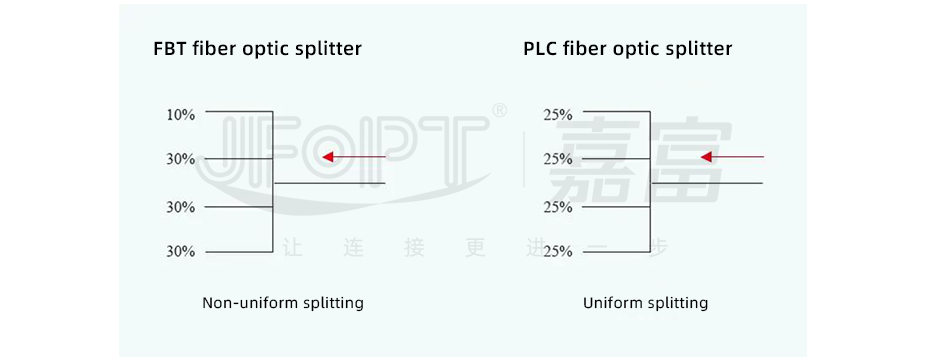
▶ Failure Rate
Due to the limitations of the mature tapering technology, which can only achieve splitting ratios of 1x4 or below, FBT optical splitters require multiple 1x2 units connected in series to achieve higher splitting ratios beyond 1:8. This complex structure is more prone to errors, increasing the likelihood of failure. Consequently, the higher the splitting ratio of an FBT optical splitter, the greater the failure rate. In contrast, PLC optical splitters have a significantly lower failure rate compared to FBT optical splitters, as shown in the figure below.
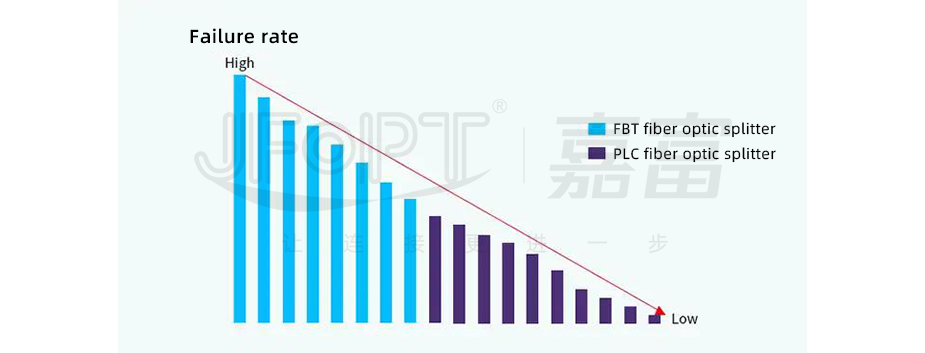
In short, PLC optical splitters and FBT optical splitters each have their own advantages and disadvantages, as detailed below:
Although PLC optical splitters and FBT optical splitters may appear similar in terms of appearance and size, they differ significantly in manufacturing processes, working wavelengths, and temperature adaptability. The advent of PLC optical splitters represents a significant advancement in splitter technology. Compared to traditional FBT optical splitters, PLC optical splitters offer superior performance. If your network has higher performance requirements, it is advisable to choose PLC optical splitters over FBT optical splitters.